Introduction
Effective inventory control is a delicate balance between maintaining adequate stock levels to meet customer demand while avoiding the pitfalls of stockouts and overstocking. Both scenarios can have significant financial and operational repercussions for businesses. In this blog, we will delve into the strategies and best practices that organizations can adopt to strike the right equilibrium, ensuring optimal inventory levels and minimizing the risks associated with stockouts and overstocking.
In the dynamic business landscape of Texas, where the demand for efficient supply chain management is ever-growing, effective inventory control is crucial for businesses aiming to strike the delicate balance between minimizing stockouts and avoiding overstocking. From the bustling warehouses in Houston to the strategic distribution centers in Dallas, businesses in the Lone Star State must employ robust strategies to optimize their inventory levels. This article explores key strategies for inventory control, emphasizing the importance of advanced technologies, strategic partnerships, and data-driven decision-making in warehousing operations in Texas.
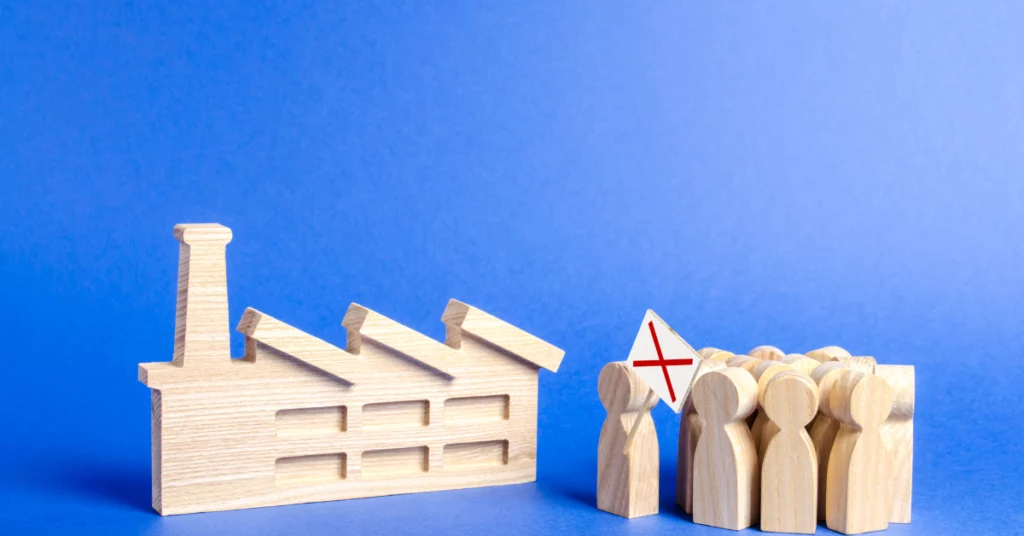
Table of Contents
The Costly Conundrum: Stockouts and Overstocking
Stockouts occur when demand exceeds supply, leading to unfulfilled orders, frustrated customers, and potential loss of sales. On the other hand, overstocking involves holding excess inventory, tying up capital, and incurring storage costs, with the added risk of obsolescence. Both situations can lead to decreased profitability, operational inefficiencies, and strained customer relationships.
Strategies for Minimizing Stockouts
Accurate Demand Forecasting:
Precise demand forecasting is the foundation of effective inventory control. Utilize historical data, market trends, and advanced analytics to anticipate customer needs and fluctuations in demand accurately.
Safety Stock:
Maintain a safety stock – a buffer of inventory – to account for unexpected demand spikes, supply chain disruptions, or delays. This safety net helps prevent stockouts during unforeseen circumstances.
Supplier Collaboration:
Forge strong relationships with suppliers. Open communication and collaboration can lead to better lead times, reliable deliveries, and improved coordination in managing demand fluctuations.
Implement Just-in-Time (JIT):
JIT inventory management focuses on receiving goods only as needed, minimizing excess inventory on hand. This approach can reduce storage costs and the likelihood of stockouts.
Automated Replenishment:
Implement automated inventory replenishment systems that trigger orders when stock levels reach predetermined thresholds. This ensures timely replenishment and reduces the risk of stockouts.
Leveraging Advanced Technologies for Real-Time Visibility:
Warehouses in Houston and across Texas can benefit significantly from the implementation of advanced technologies that provide real-time visibility into inventory levels. Incorporating Warehouse Management Systems (WMS), RFID tagging, and barcode scanning systems enables accurate and up-to-date tracking of inventory. This real-time visibility minimizes the risk of stockouts by allowing businesses to respond promptly to changes in demand, ensuring that products are always available when needed.
Implementing Just-in-Time (JIT) Inventory Practices:
Just-in-Time (JIT) inventory practices are an effective strategy to minimize overstocking while ensuring that sufficient stock is available to meet customer demand. By synchronizing inventory levels with actual demand, businesses can reduce holding costs and the risk of obsolete inventory. JIT practices are particularly relevant in the dynamic market environment of Texas, allowing businesses to stay agile and responsive to fluctuations in demand.
Strategic Warehouse Placement for Efficient Distribution:
Strategic placement of warehouses in Texas is pivotal for optimizing inventory distribution. Warehouses in Houston and Dallas, when strategically located, can cater to diverse markets efficiently. This not only reduces transit times and transportation costs but also ensures that products are positioned closer to consumers, minimizing the risk of stockouts and enhancing overall supply chain responsiveness.
Collaborating with Freight Forwarders in Dallas and Logistics Companies in Texas:
Collaboration with freight forwarders in Dallas and logistics companies across Texas is instrumental in achieving efficient transportation and distribution. By partnering with these entities, businesses can optimize transportation routes, reduce transit times, and ensure timely replenishment of inventory. This collaborative approach enhances the accuracy of inventory forecasts, minimizing the likelihood of stockouts and contributing to cost-effective supply chain operations.
Data-Driven Decision-Making for Inventory Optimization:
In the era of big data, leveraging analytics and data-driven decision-making is paramount for effective inventory control. Analyzing historical sales data, monitoring market trends, and utilizing forecasting tools enable businesses to make informed decisions about inventory levels. This proactive approach minimizes the risk of both stockouts and overstocking, aligning inventory levels closely with actual demand.
Strategies for Avoiding Overstocking
- ABC Analysis: Categorize products based on their value and turnover rates using the ABC analysis method. This enables you to prioritize inventory control efforts and avoid overstocking less critical items.
- Demand Forecasting Accuracy: Inaccurate demand forecasting can lead to overstocking. Regularly analyze and fine-tune your forecasting methods to align with actual customer demand.
- Promotion and Seasonal Planning: Carefully plan for promotions and seasonal fluctuations in demand. Adjust inventory levels accordingly, ensuring that excess stock is not left unused after peak periods.
- Implement Economic Order Quantity (EOQ): EOQ calculates the optimal order quantity that minimizes total inventory costs, including holding costs and ordering costs. This helps prevent overstocking while ensuring efficient ordering practices.
- Real-Time Inventory Visibility: Employ inventory management software or systems that offer real-time visibility into inventory levels, order statuses, and sales trends. This empowers accurate decision-making and prevents overordering.
Integrated Solutions for Balanced Inventory Control
- Inventory Management Software (IMS): IMS provides centralized control over inventory levels, order processing, and demand forecasting. It offers real-time insights for informed decision-making.
- Point-of-Sale (POS) Integration: Integrating POS systems with inventory management helps track sales trends, enabling proactive adjustments to inventory levels based on actual customer purchasing patterns.
- Collaborative Planning, Forecasting, and Replenishment (CPFR): CPFR involves collaboration between suppliers and retailers in demand forecasting and inventory planning, leading to more accurate replenishment decisions.
- Advanced Analytics and AI: Utilize predictive analytics and artificial intelligence to forecast demand, analyze market trends, and identify potential overstocking or stockout risks.
Best Practices for Effective Inventory Control
- Regular Audits: Conduct routine physical inventory counts to verify accuracy and identify discrepancies. This helps prevent errors in demand forecasting and overstocking.
- Set Reorder Points: Establish reorder points for each item, indicating the level at which a new order should be placed. This prevents stockouts while avoiding unnecessary stock accumulation.
- Continuous Monitoring: Continuously monitor sales trends, stock turnover rates, and market dynamics. This proactive approach allows you to adjust inventory levels based on changing demand.
- Data-Driven Decision-Making: Base inventory decisions on data rather than gut feelings. Incorporate historical data, market trends, and demand patterns for accurate planning.
- Cross-Functional Collaboration: Foster collaboration between departments, including sales, marketing, and supply chain management. This ensures alignment between inventory levels and expected demand.
Inventory control is a critical aspect of any successful business operation. By employing strategies to minimize stockouts and overstocking, organizations can achieve a delicate balance that enhances customer satisfaction, reduces costs, and optimizes resource utilization.
Through accurate demand forecasting, safety stock management, supplier collaboration, and technological integration, businesses can avoid the negative impact of stockouts and overstocking on profitability and operational efficiency. With the right approach and a commitment to data-driven decision-making, businesses can navigate the complex landscape of inventory control and set themselves up for sustainable growth and success in the competitive market.
In the competitive landscape of Texas, where efficient supply chain management is integral to success, businesses must prioritize effective inventory control to minimize stockouts and overstocking. Leveraging advanced technologies, implementing JIT inventory practices, strategically placing warehouses, collaborating with freight forwarders and logistics companies, and embracing data-driven decision-making are key strategies for achieving optimal inventory levels. By adopting these approaches, businesses in Houston, Dallas, and throughout Texas can enhance their supply chain resilience, improve customer satisfaction, and ultimately maximize their operational efficiency.