Introduction
Warehouse operations are the heartbeat of supply chain management, serving as the pivotal hub for inventory storage, order fulfillment, and distribution. In an era where efficiency and cost-effectiveness are paramount, optimizing warehouse operations becomes a strategic imperative. This blog explores a comprehensive range of strategies and best practices to reduce costs and enhance efficiency in warehouse operations, ultimately contributing to improved profitability and customer satisfaction.
In the heart of the bustling Texan business landscape, optimizing warehouse operations is crucial for businesses looking to stay competitive. From the thriving warehouses in Houston to the strategic distribution centers in Dallas, the efficient management of these facilities plays a pivotal role in meeting customer demands and reducing operational costs. This article explores key strategies for streamlining operations in Texas, emphasizing the importance of advanced technologies, Warehouse Management Systems (WMS), and collaboration with freight forwarders and logistics companies.
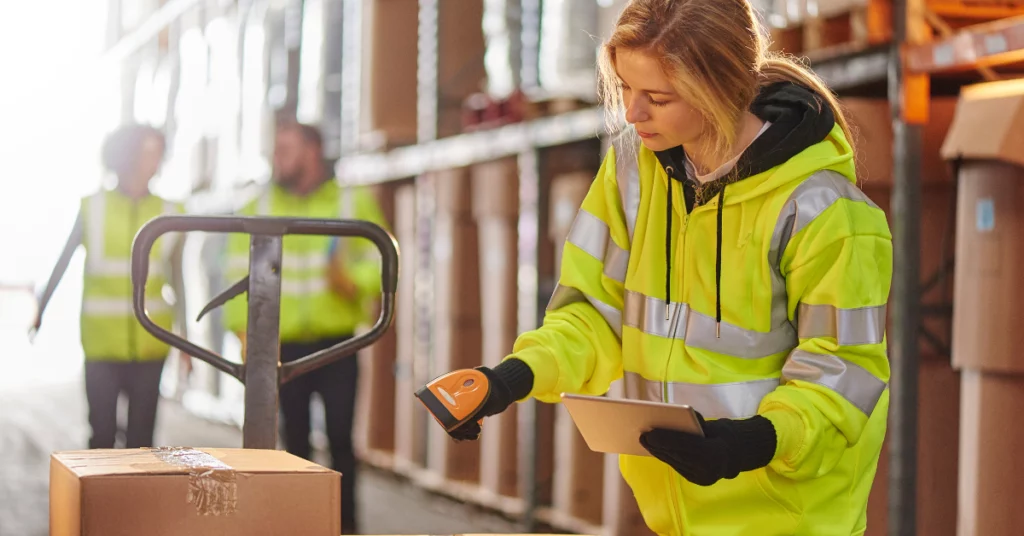
Table of Contents
The Intersection of Cost Reduction and Efficiency
Efficiency and cost reduction are two sides of the same coin in warehouse operations. While cost reduction aims to minimize expenses, efficiency focuses on optimizing processes for maximum output with minimal waste. Achieving a harmonious balance between these two factors is essential for sustained success.
Streamlining Warehouse Layout and Design
Optimal Space Utilization:
Efficient space utilization is a cornerstone of warehouse management. Employ techniques such as vertical racking, mezzanine floors, and compact storage systems to maximize storage density.
Zoning and Segmentation:
Divide the warehouse into functional zones, aligning with the layout of goods and order processing stages. This minimizes travel distances, reducing time and effort.
Ergonomic Design:
Create a workspace that prioritizes employee safety and comfort. Ergonomically designed workstations and equipment minimize strain and fatigue, leading to higher productivity.
Leveraging Technology for Automation
- Warehouse Management Systems (WMS): A robust WMS streamlines operations by managing inventory, orders, and shipments. Real-time data visibility enhances decision-making and reduces errors.
- Barcode Scanning and RFID: Implementing automated identification methods like barcode scanning and RFID technology reduces manual data entry errors and expedites order processing.
- Automated Material Handling: Technologies such as conveyors, automated guided vehicles (AGVs), and robotics streamline material movement, reducing labor-intensive tasks and increasing accuracy.
Demand Forecasting and Inventory Management(Warehouse Operations)
- Data-Driven Forecasting: Leverage historical sales data, market trends, and predictive analytics to refine demand forecasts. This prevents overstocking and understocking scenarios.
- ABC Analysis: Prioritize inventory based on value, ensuring that high-value items receive more attention in terms of storage and picking strategies.
- Just-In-Time (JIT) Inventory: Adopting JIT principles minimizes excess inventory by aligning procurement with actual demand, reducing carrying costs.
Efficient Order Picking and Fulfillment
- Batch and Zone Picking: Combine orders into batches and assign specific zones for picking. This minimizes travel time and optimizes picking routes.
- Pick-to-Light and Put-to-Light Systems: These systems use visual cues to guide workers through the picking and putting processes, enhancing accuracy and speed.
- Voice Picking: Hands-free, voice-guided picking systems improve efficiency by providing instructions to workers in real-time.
Workforce Optimization and Training
- Cross-Training Employees: Cross-train employees across various warehouse tasks to increase flexibility and responsiveness during peak periods.
- Performance Metrics and Incentives: Set clear performance metrics and offer incentives for achieving targets, motivating employees to work efficiently.
- Continuous Training and Skill Development: Invest in ongoing training to keep employees updated on new technologies and best practices.
Sustainability Initiatives
- Energy-Efficient Lighting and Equipment: Use energy-efficient lighting and equipment to reduce operational costs and minimize environmental impact.
- Eco-Friendly Packaging: Opt for sustainable packaging materials that reduce waste and align with eco-conscious consumer preferences.
- Waste Reduction Strategies: Implement recycling programs and waste reduction initiatives to minimize the environmental footprint of warehouse operations.
Real-time Tracking and Data Analytics
Harness real-time tracking systems and data analytics to monitor key performance indicators (KPIs) such as order processing times, inventory turnover rates, and workforce productivity.
Continuous Improvement and Kaizen
Embrace the philosophy of continuous improvement and Kaizen. Encourage employees to identify bottlenecks, suggest process enhancements, and implement incremental changes for ongoing optimization.
Utilizing Advanced Technologies in Warehouses in Houston:
Warehouses in Houston, being central to various industries, benefit immensely from the adoption of advanced technologies. Automated systems, such as robotics and conveyors, enhance order fulfillment processes, reducing labor costs and increasing operational efficiency. RFID and barcode scanning systems, when integrated into warehouse operations, contribute to accurate inventory tracking, minimizing errors and streamlining overall logistics processes.
Implementing Warehouse Management Systems (WMS) in Texas Warehouses:
Warehouse Management Systems are instrumental in optimizing operations in warehouses across Texas. Whether in Houston or other parts of the state, a WMS provides real-time visibility into inventory, automates routine tasks, and enhances order processing. By centralizing data and automating workflows, WMS software reduces manual errors, increases order accuracy, and improves the overall efficiency of warehouse operations.
Strategic Warehouse Placement in Texas:
Selecting the right location for warehouses in Texas is paramount for optimizing logistics networks. Whether establishing a warehouse in Houston or elsewhere in the state, strategic placement ensures proximity to key markets and efficient transportation routes. This minimizes transit times, reduces transportation costs, and enhances the overall responsiveness of the supply chain.
Collaborating with Freight Forwarders in Dallas:
Dallas, as a major logistics hub, hosts numerous distribution warehouses. Collaborating with freight forwarders in Dallas is essential for optimizing transportation routes and reducing transit times. A seamless partnership ensures that goods move efficiently from warehouses to distribution centers, meeting customer expectations and minimizing transportation costs.
Engaging Logistics Companies in Texas:
Logistics companies in Texas play a crucial role in coordinating the movement of goods across the state. Efficient collaboration with these companies ensures smooth operations, from warehousing in Houston to distribution centers in Dallas. Clear communication and data sharing through integrated systems enhance visibility and allow for the optimization of transportation routes, ultimately reducing costs and increasing overall supply chain efficiency.
The Nexus of Cost Savings and Operational Excellence
Reducing costs and enhancing efficiency in warehouse operations is a holistic endeavor that involves a synergy of strategic planning, technological integration, and workforce empowerment. The convergence of these elements results in streamlined processes, reduced waste, and increased customer satisfaction.
In the dynamic landscape of supply chain management, warehouse operations play a pivotal role in shaping a business’s success. By diligently implementing the strategies outlined in this guide, organizations can foster a culture of efficiency, minimize costs, and elevate their operational excellence. Remember, the journey to reduced costs and increased efficiency is an ongoing one, requiring adaptability, innovation, and a commitment to continuous improvement.
In the dynamic business environment of Texas, optimizing warehouse operations is fundamental to success. Leveraging advanced technologies, implementing Warehouse Management Systems, strategically placing warehouses, and fostering collaboration with freight forwarders and logistics companies are key strategies for streamlining operations. Whether in Houston or Dallas, businesses that prioritize efficiency in their warehousing operations are better positioned to meet the challenges of a rapidly evolving market, reduce costs, and deliver exceptional service to their customers.