Lean manufacturing is a systematic approach that focuses on eliminating waste, optimizing processes, and enhancing overall efficiency in production operations. When applied to kitting and assembly processes, lean principles offer numerous benefits, enabling manufacturers to streamline workflows, improve productivity, and deliver high-quality products. In this article, we will explore the advantages of implementing lean manufacturing in kitting and assembly operations.
In the dynamic landscape of Texas warehousing, lean manufacturing principles are increasingly gaining prominence, especially in kitting and assembly processes. From the bustling warehouses in Houston to the strategically located distribution centers in Dallas, adopting lean manufacturing practices in kitting and assembly offers a myriad of benefits. This article explores the advantages of implementing lean manufacturing principles in the context of Texas warehousing, emphasizing the keywords associated with logistics and supply chain management.
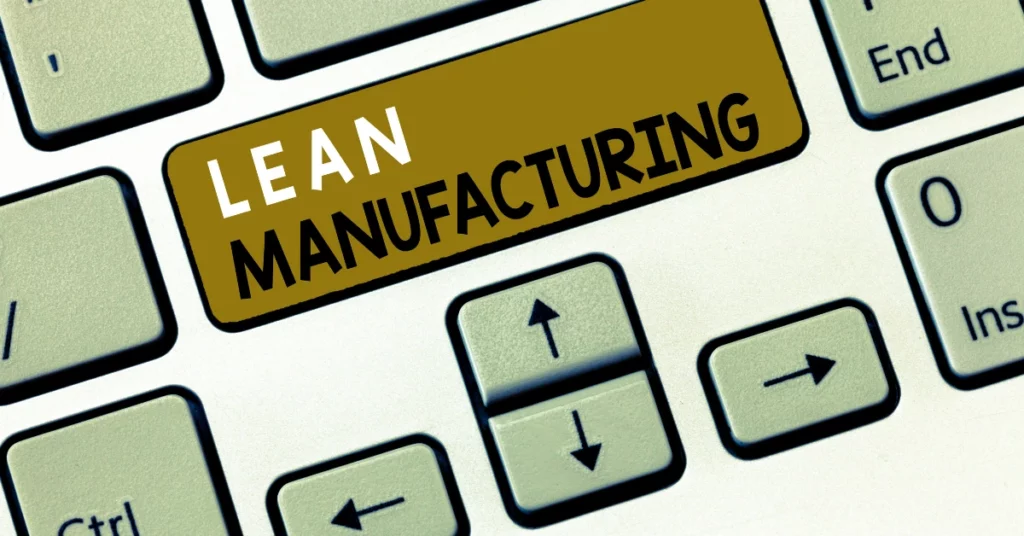
Table of Contents
Understanding Lean Manufacturing
Lean manufacturing is a systematic approach to reducing waste and optimizing efficiency in production processes. Originally derived from the Toyota Production System, lean principles are now widely applied across industries to enhance productivity and streamline operations.
Waste Reduction:
Lean manufacturing aims to identify and eliminate various types of waste, including overproduction, excess inventory, unnecessary motion, waiting time, and defects. By reducing waste in kitting and assembly, manufacturers can optimize resource utilization, save costs, and improve overall efficiency.
Enhanced Productivity:
Lean principles focus on simplifying and streamlining processes. By minimizing non-value-added activities, kitting and assembly tasks become more efficient and less time-consuming. As a result, workers can produce more output in less time, leading to higher productivity levels.
Improved Quality:
Lean manufacturing emphasizes the importance of defect prevention and continuous improvement. By detecting and addressing quality issues early in the process, manufacturers can reduce the likelihood of defects, rework, and customer returns. This leads to higher product quality and increased customer satisfaction.
Smoother Workflows:
Through value stream mapping and process optimization, lean manufacturing helps identify bottlenecks and inefficiencies in kitting and assembly operations. By addressing these issues, workflows become smoother, and production can flow more seamlessly from one stage to the next.
Flexibility and Responsiveness:
Lean manufacturing encourages a focus on customer value and responsiveness to changing demands. Manufacturers can adjust kitting and assembly processes quickly to accommodate shifts in customer preferences or production requirements. This flexibility enhances the company’s ability to adapt to market changes effectively.
Employee Empowerment and Engagement (Lean manufacturing)
Lean principles involve empowering employees at all levels to actively participate in process improvement. Workers are encouraged to identify issues, suggest solutions, and take ownership of their work. This engagement fosters a sense of pride and satisfaction, leading to a more motivated and dedicated workforce.
Cost Savings:
By eliminating waste and optimizing processes, lean manufacturing reduces costs associated with excess inventory, defects, overproduction, and unnecessary labor. These cost savings contribute to increased profitability and a more competitive position in the market.
Safer Work Environment:
Lean manufacturing promotes workplace organization and the elimination of hazards. By minimizing clutter and unnecessary movement, the risk of accidents and injuries in kitting and assembly operations is reduced, creating a safer work environment for employees.
Benefits of Lean Manufacturing in Kitting and Assembly
- Minimized Waste:
Lean manufacturing in kitting and assembly significantly reduces waste, both in terms of time and resources. Warehouses in Houston and Dallas, among others in Texas, are adopting lean practices to eliminate unnecessary movements, waiting times, and excess inventory. This leads to a more efficient utilization of resources and a reduction in operational costs.
- Improved Productivity:
Lean manufacturing emphasizes continuous improvement and the elimination of non-value-added activities. In kitting and assembly, this translates to streamlined processes, reduced downtime, and improved cycle times. Warehouses in Texas benefit from enhanced productivity as a result, allowing for increased output without compromising quality.
- Enhanced Flexibility:
Lean manufacturing principles promote flexibility and adaptability in response to changing demands. Warehouses in Texas, where market dynamics can be diverse, find that lean practices in kitting and assembly enable them to adjust production quickly and efficiently. This flexibility ensures that warehouses can respond promptly to shifts in customer demand and market trends.
- Optimized Space Utilization:
Efficient use of space is a crucial aspect of lean manufacturing. Warehouses in Houston and Dallas, where real estate may be at a premium, benefit from lean practices that optimize the layout and organization of kitting and assembly areas. This results in reduced travel distances, minimized storage space requirements, and overall improved space utilization.
- Increased Quality:
Lean manufacturing places a strong emphasis on quality control. In kitting and assembly, this means detecting and addressing defects early in the process, preventing them from propagating through the supply chain. The result is higher-quality products, reduced rework, and enhanced customer satisfaction.
- Collaboration with Logistics Partners:
Lean manufacturing extends beyond the warehouse to involve collaboration with logistics partners. Freight forwarders in Dallas and logistics companies across Texas play a crucial role in ensuring the smooth flow of materials and finished products. Lean principles, when applied collaboratively, contribute to efficient transportation, reduced lead times, and an overall synchronized supply chain.
Continuous Improvement Culture:
Lean manufacturing establishes a culture of continuous improvement, where small incremental changes are valued and encouraged. This culture fosters ongoing innovation and ensures that kitting and assembly processes are continuously refined for maximum efficiency and effectiveness.
Unlocking Benefits in Kitting and Assembly Operations:
The adoption of lean manufacturing principles in kitting and assembly operations offers significant benefits for manufacturers. From waste reduction and enhanced productivity to improved product quality and employee engagement, lean practices create a more efficient and agile production environment. By embracing a culture of continuous improvement and empowering their workforce, companies can achieve sustainable success and maintain a competitive edge in the dynamic manufacturing landscape.
In the competitive world of Texas warehousing, adopting lean manufacturing principles in kitting and assembly processes brings a multitude of benefits. From minimizing waste and improving productivity to enhancing flexibility and collaboration with logistics partners, lean practices contribute to the overall efficiency and success of warehousing operations. As warehouses in Houston, Dallas, and across Texas embrace lean manufacturing, they position themselves for sustained growth and resilience in the ever-evolving landscape of logistics and supply chain management.
For more information, feel free to get in touch with us. Our dedicated team is ready to assist you with any inquiries or details you may need. Whether you have questions about our products, services, or want to discuss specific requirements for your projects, we are here to help.