Introduction
In the fast-paced world of modern business, optimizing warehouse layout has become a strategic imperative for efficient inventory management. A well-designed warehouse layout can significantly impact operational efficiency, order fulfillment speed, and overall cost-effectiveness. This blog explores the essential tips and best practices for optimizing warehouse layout to enhance inventory management, streamline processes, and maximize operational excellence.
In the dynamic landscape of warehousing and logistics in Houston, Texas, efficient inventory management is the key to success. A well-optimized warehouse layout can significantly enhance operational efficiency, reduce costs, and improve overall productivity. This article explores essential tips for optimizing your warehouse layout, with a focus on the thriving logistics hub of Houston and neighboring areas in Texas.
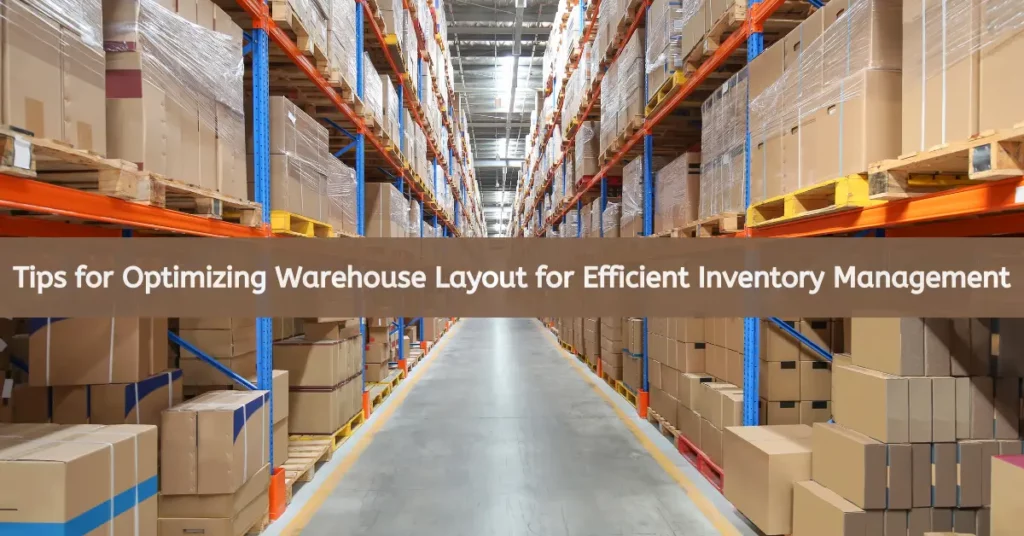
Table of Contents
The Significance of Warehouse Layout Optimization
A carefully planned optimizing warehouse layout goes beyond just organizing shelves and storage spaces. It directly affects productivity, reduces errors, and ensures that inventory is easily accessible and efficiently managed. A poorly designed layout can lead to wasted time, increased labor costs, and operational inefficiencies.
Essential Tips for Optimizing Warehouse Layout
- Analyze Inventory Characteristics: Before designing your warehouse layout, understand the characteristics of your inventory. Identify high-demand items, slow-moving stock, and any items that require special storage conditions. Categorizing inventory helps in determining the most suitable storage methods.
- Utilize ABC Analysis: Employ the ABC analysis method to categorize items based on their value and turnover rate. High-value, fast-moving items should be located in easily accessible areas to reduce picking times, while low-value items can be stored in less accessible areas.
- Implement Efficient Slotting: Slotting involves assigning specific storage locations to individual items based on their characteristics. Group similar items together to minimize travel time during order picking. Consider factors like weight, size, and demand frequency.
- Design Clear Traffic Flow: Plan for a clear and efficient traffic flow within the warehouse. Create designated pathways for forklifts, pallet jacks, and personnel to prevent congestion and accidents. Minimize intersections and ensure pathways are wide enough for easy movement.
- Maximize Vertical Space: Vertical space is often underutilized. Incorporate tall shelving units and consider installing mezzanines to maximize vertical storage. Utilize vertical space for slow-moving or seasonal items, keeping frequently accessed items at eye level.
- Prioritize Fast-Moving Items: Place high-demand items closer to shipping areas to reduce picking and packing time. This minimizes the distance traveled and increases overall order fulfillment speed.
- Designated Receiving and Shipping Areas: Clearly define separate areas for receiving and shipping. This prevents confusion, reduces cross-traffic, and ensures smooth transitions between inbound and outbound processes.
- Use Technology for Guidance: Implement technologies like barcode scanners, RFID systems, and warehouse management software to guide inventory movement. These technologies enhance accuracy, reduce errors, and improve overall efficiency.
- Flexible Layout Design: Design a flexible layout that can adapt to changing business needs. As your inventory and business operations evolve, the warehouse layout should be easily adjustable to accommodate new requirements.
- Safety Considerations: Prioritize safety by incorporating proper lighting, signage, and emergency exit routes. Ensure that heavy items are stored securely and that workers are trained on safe handling practices.
Streamlining Operations: Key Tips for Optimizing Warehouse Layout in Houston, Texas
- Strategic Zoning for Products: Organize your warehouse space strategically by zoning areas for specific types of products. Consider factors such as product velocity, size, and storage requirements. This ensures that high-demand items are easily accessible, reducing picking and packing times.
- Utilize Vertical Space: Maximize your warehouse’s vertical space by implementing tall shelving units and mezzanines. This allows for better use of square footage and creates additional storage capacity, a crucial aspect in bustling locations like Houston.
- Efficient Picking Paths: Design picking paths that minimize travel time for warehouse staff. Group commonly picked items together and arrange the layout to facilitate a logical order for picking, packing, and shipping.
- Utilize Technology: Invest in warehouse management systems (WMS) and other technology solutions to streamline inventory tracking and order processing. Automation tools can help reduce errors, increase accuracy, and boost overall efficiency.
- Flexibility for Growth: Plan your warehouse layout with scalability in mind. Ensure that the design allows for easy expansion or modification to accommodate the growing demands of your business and the dynamic logistics landscape in Houston, Texas.
- Optimized Receiving and Shipping Areas: Design efficient receiving and shipping areas to prevent bottlenecks. Properly place these zones to facilitate smooth transitions from incoming shipments to storage and from storage to outbound shipments.
- Temperature Control for Specialized Products: If your inventory includes temperature-sensitive items, designate appropriate storage areas with climate control. This is particularly relevant in the diverse climate of Texas, where temperature variations can impact certain products.
- Collaborate with Dallas Distribution Warehouses: Leverage the strategic location of Dallas distribution warehouses for cost-effective logistics solutions. Establish partnerships with freight forwarders and logistics companies in Texas to enhance your distribution network and improve shipping efficiency.
- Regular Evaluation and Adjustment: Continuously monitor and evaluate the effectiveness of your warehouse layout. Solicit feedback from staff, track key performance indicators, and be ready to make adjustments as needed to optimize operations.
Benefits of an Optimized Warehouse Layout
- Improved Productivity: An warehouse layout optimization reduces travel time, minimizes congestion, and enhances overall workflow. This leads to increased productivity and faster order processing.
- Enhanced Accuracy: A well-organized layout with clear signage and designated storage locations reduces the chances of errors in picking and packing.
- Space Utilization: Maximizing available space helps in accommodating more inventory without the need for expansion, thus optimizing storage costs.
- Faster Order Fulfillment: With high-demand items strategically placed, the time required to pick and pack orders is reduced, leading to quicker order fulfillment.
- Reduced Labor Costs: Efficient layout design reduces unnecessary movement, resulting in lower labor costs and improved resource utilization.
- Customer Satisfaction: Faster order processing and accurate inventory management lead to improved customer satisfaction due to on-time deliveries and reduced backorders.
Best Practices for Implementing Warehouse Layout Changes
Collaborate Across Teams:
Involve personnel from various departments in the layout design process to ensure that all needs are considered and integrated.
Phased Implementation:
If possible, implement layout changes in phases to minimize disruptions to ongoing operations.
Regular Evaluation:
Continuously monitor and assess the effectiveness of the new layout. Seek feedback from employees and be open to making adjustments as needed.
Invest in Training:
Properly train employees on the new layout and any technology implementations. Familiarity with the new setup is essential for smooth operations.
Future-Proof Design:
Anticipate future growth and changes in inventory patterns when designing the layout. This ensures that the layout remains relevant and effective over time.
Conclusion
An optimized warehouse layout is a strategic investment that can yield substantial benefits in terms of operational efficiency, cost savings, and customer satisfaction. By considering inventory characteristics, traffic flow, technology integration, and safety measures, businesses can design a layout that maximizes space, minimizes errors, and accelerates order fulfillment.
Regular evaluation and a willingness to adapt ensure that the layout remains aligned with evolving business needs. As technology continues to shape the future of logistics, an intelligently designed warehouse layout becomes a competitive advantage that enhances overall inventory management and contributes to the success of the entire supply chain.
In the thriving logistics and warehousing landscape of Houston, Texas, an optimized warehouse layout is a critical component of success. By implementing strategic zoning, utilizing vertical space, incorporating technology, and fostering flexibility, businesses can enhance inventory management efficiency. Collaborating with distribution centers in Texas and staying adaptable to the dynamic market conditions further solidifies your position in this bustling logistics hub. With these tips, your warehouse can become a well-oiled machine, ready to meet the demands of the competitive Texas market.